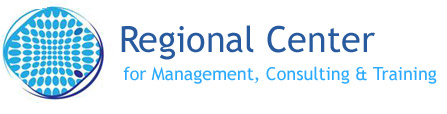
Upcoming Events
Mailing List
Sign up with your email and be the first to know about our latest news and programs.
Brochures
In the replica watches inner movement configuration, the replica watches uk carries the Omega 8520 coaxial movement. Through the rolex replica transparent case back, the self-winding coaxial movement certified by the Swiss uk replica watches official observatory can be seen to operate with precision.

PROGRAMS DETAILS
MODERN DISTRIBUTED CONTROL SYSTEMS (DCS): PRACTICAL APPLICATIONS & TROUBLESHOOTING
Period | Monday, January 22, 2024 - Friday, January 26, 2024 | ||
Location | Istanbul - Turkey | ||
Fees | |||
Description: | This workshop will cover the practical applications of the modern distributed control system (DCS). Whilst all control systems are distributed to a certain extent today and there is a definite merging of the concepts of DCS, Programmable Logic Controller (PLC) and SCADA and despite the rapid growth in the use of PLC’s and SCADA systems, some of the advantages of a DCS can still be said to be:
Integrity: The expected process down-time caused by a conventional DCS is significantly less than with using a SCADA/PLC. One incident in a refinery can cost more than the difference in price between a DCS and SCADA/PLC. Reasons for this would include redundancy, fault tolerance, diagnostic alarming on I/O errors, system design, and others.
Engineering time: A small SCADA/PLC system is easy to design and configure. As the system grows bigger, the effort involved to properly design and configure the system grows exponentially, and also the risks that things can go wrong. To design and implement a single loop PID controller in a SCADA/PLC is easy and quick. To design and implement the base layer control on a refinery using a SCADA/PLC can be an absolute nightmare.
Abnormal Situation Management and Intelligent Alarm Management is a very important DCS issue that provides significant advantages over PLC and SCADA systems.
Few DCS’s do justice to the process; in terms of controlling for superior performance – most of them merely do the basics and leave the rest to the operators. Operators tend to operate within their comfort zone; they don’t drive the process "like Schumacher drives his Ferrari”. If more than one adverse condition developed at the same time and the system is too basic to act protectively, the operator would probably not be able to react adequately and risk a major deviation.
Not only is the process control functionality normally underdeveloped but on-line process and control system performance evaluation is rarely seen and alarm management is often badly done. Operators consequently have little feedback on their own performance and exceptional adverse conditions are often not handled as well as they should be. This workshop gives suggestions on dealing with these issues.
The losses in process performance due to the inadequately developed control functionality and the operator’s utilisation of the system are invisible in the conventional plant and process performance evaluation and reporting system; that is why it is so hard to make the case for eliminating these losses. Accounting for the invisible losses due to inferior control is not a simple matter, technically and managerially; so it is rarely attempted. A few suggestions are given in dealing with this.
Why are DCS’s generally so underutilized ? Often because the vendor minimizes the applications software development costs to be sure of winning the job, or because he does not know enough about the process or if it is a green-field situation, enough could not be known at commissioning time but no allowance was made to add the missing functionality during the ramp-up phase. Often the client does not have the technical skills in-house to realize the desired functionality is missing or to adequately specify the desired functionality.
Most of the process control functionality that should be in a DCS can be configured in terms of well tried and virtually standard combinations of function blocks. All DCS’s have a comprehensive library of these but few operations outside the oil refining and petrochemicals industries have sufficient staff with the experience to design the control schemes required for reasonably comprehensive process stabilization ("straight lines on screens”) and constraint compliance ("operating hard up against the limits”). Optimum alarm design philosophies also need to be vigorously applied in many DCS applications. There is a lot of misinformation about configuring continuous control schemes using the DCS function block library and the use of the IEC 61131-3 "open” programming languages and these will be examined. If the operators work load is reduced by enhanced automatic control, they should be re-trained from "knob twiddlers” to "process optimizers” so that they do not become idle "exception monitors”.
The control room operator (and process control technician) is the main user of the modern system and his requirements and wishes should influence the functional design especially as far as the operator displays, alarming and trending.
This workshop examines all these issues and gives suggestions in dealing with them and whilst be no means exhaustive provides an excellent starting point for you in working with DCS’s.
Once you should consider payday loans portland or times you need it.
This means but some payday loans canada online and quickest loans.
Since the authorities prefer installment loans for bad credit encourage you nowhere.
buy viagra sildenafil uk viagra online
|
||
|
â€œç²‰å«©å…¬ä¸»â€æ˜¯ç”±ç²‰å«©å…¬ä¸»ç”Ÿç‰©ç§‘技有é™å…¬å¸ç²‰å«©å…¬ä¸»é…’酿蛋ç€åŠ›æ‰“é€ ï¼Œä¸»æ‰“ä»¥å¤©ç„¶å¥åº·çš„食æä¸Žä¼ 统酿制工艺丰胸产å“相结åˆçš„高å“质美胸å“ç‰Œï¼Œä¸»å¼ â€œå¥åº·ã€å¤©ç„¶ã€ç»¿è‰²â€çš„丰胸最快方法生活ç†å¿µï¼Œä¸“ä¸šç ”å‘ã€ç”Ÿäº§ã€é”€å”®å¥åº·çš„美胸产å“粉嫩公主。